Sensational Info About How To Reduce Downtime
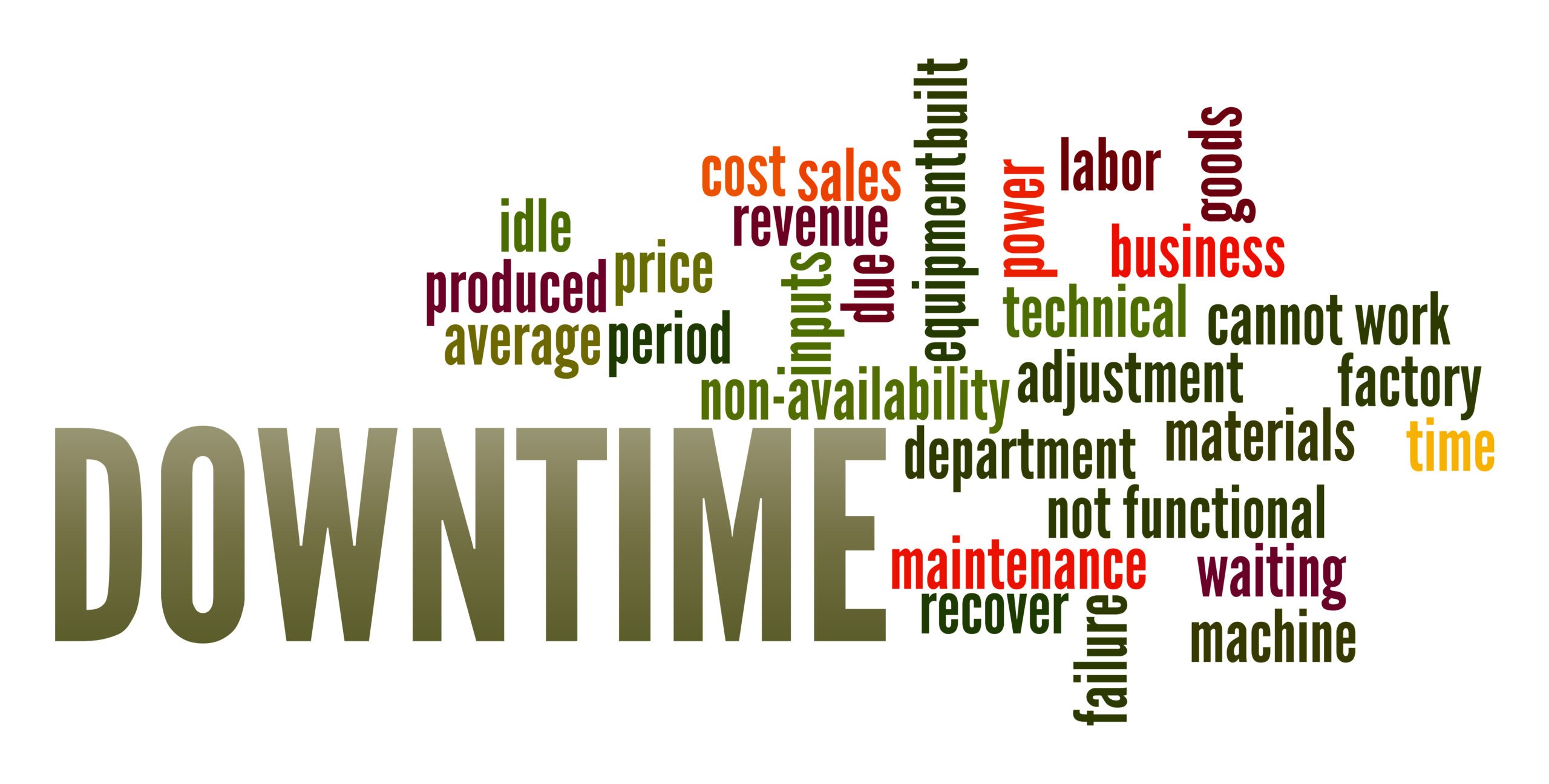
Here are five ways you can reduce downtime in the workplace.
How to reduce downtime. In order to minimize downtime, staff members need to be able to address issues and communicate them to other departments so that the appropriate members of the team. 8 top tips from owners and executives 1. Plan ahead your maintenance policy one of the sure shot ways you can prepare your company for downtime is.
The link between compliance and downtime; Train employees & gather their. In order to reduce machine downtime, expand your maintenance strategy to include predictive maintenance elements.
Proactive prevention can be an effective strategy. A slow work order process. The most efficient way to reduce machine downtime is to employ manufacturing downtime tracking software or a predictive maintenance tool.
Establishing more effective triggers and flagging prominent issues can increase asset efficiency and reduce downtime from breakdowns. Staff communications between managers and employees is proven to be essential. The constant stream of data from these attached.
Nearly half of manufacturing companies admit. Production monitoring is the surest step to take to reduce downtime. Move to the cloud 2.
Being preventative in your approach to maintenance can also help reduce the cost of reactively having to repair a failed piece of equipment. Conduct a risk audit 4. Here are the most common ways to reduce downtime: